SÅ SKAPADES VÄRLDENS STÖRSTA SEGEL
SÅ SKAPADES VÄRLDENS STÖRSTA SEGEL
Få en inblick i designerns, duktillverkarens och segelmakarnas arbete med Perseus^3:s nya gennaker – som är stor som tio tennisplaner.

”Det är väsentligt större än allt annat där ute”, säger Glenn Cook. Han är designer av segel till superyachts och ringer från St Barth, där han testseglar seglet för allra första gången. Det är en process som han beskriver som både ”nervpåfrestande” och ”den bästa delen av jobbet”. Att utveckla och producera detta 2604 kvadratmeter stora A2-segel har nämligen krävt en massa människors medverkan, en massa tid och en massa resurser.
Processen har krävt ett omfattande arbete av ett designteam i USA och en specialbeställd duk som det tog Contender Sailcloth åtta veckor att få fram. Och själva produktionen tog mer än 15 dagar för tio segelmakare.
”Teamet bakom båten var uttryckligen ute efter ett segel som skulle prestera väl i förhållande till mätetalet”, förklarar Cook. ”Så designen fick styras av det. Och eftersom Perseus^3 är en väldigt stor båt (hon är 58,6 meter lång), svarar hon inte så snabbt på roderrörelser. Även justeringar i trim tar sin tid. Så det vi siktade på var ett segel med en väldigt stabil flygande form. Dessutom måste seglet kunna fungera i ett brett spektrum av förhållanden. Vi har därför gjort en mer förlåtande design än vad vi brukar göra till mindre båtar.”
De hanteringsmässiga utmaningarna var också en faktor som påverkade designen; förliket är så långt att seglet kan hamna i vattnet under gipparna. ”Vi utvecklade ett system ovanför halshornet som samlar ihop underdelen av seglet och förhindrar att det går i vattnet under en gipp.”
Grundmaterialet i seglet är Contender Sailcloths Supercote 350 – den tyngsta och starkaste duk de har – i kombination med Supercote 250 i förstärkningarna, vilket sparar lite vikt.
”Båten är gigantisk och genererar exceptionellt höga krafter”, tillägger Duncan Skinner, chef för Contender Sailcloth USA. ”Vi går från en duk som väger 32 gr/kvm till något som väger 150 gr/kvm, räknat på den Supercote 350-duk som används i den här gennakern. När vikten går upp ökar även styrkan, och det är det som krävs för ett segel i den här storleken.”
”Val av fiber är det första steget – det blev en höghållfast nylon. Därefter tittar vi på konstruktionen, exempelvis hur många fibertrådar vi ska väva in i varje riktning. När så duken är vävd kommer finishen in, och det är en knepig uppgift. Du måste färga duken innan du lägger på finishen. I finishen lägger vi på en coating som stabiliserar duken och tar ner porositeten till noll. Det är en väl beprövad kemisk process som resulterar i dukar som kan hantera den typ av krafter som uppstår på dessa gigantiska båtar.”
Skinner ler. ”Den här saken är verkligen stor!”
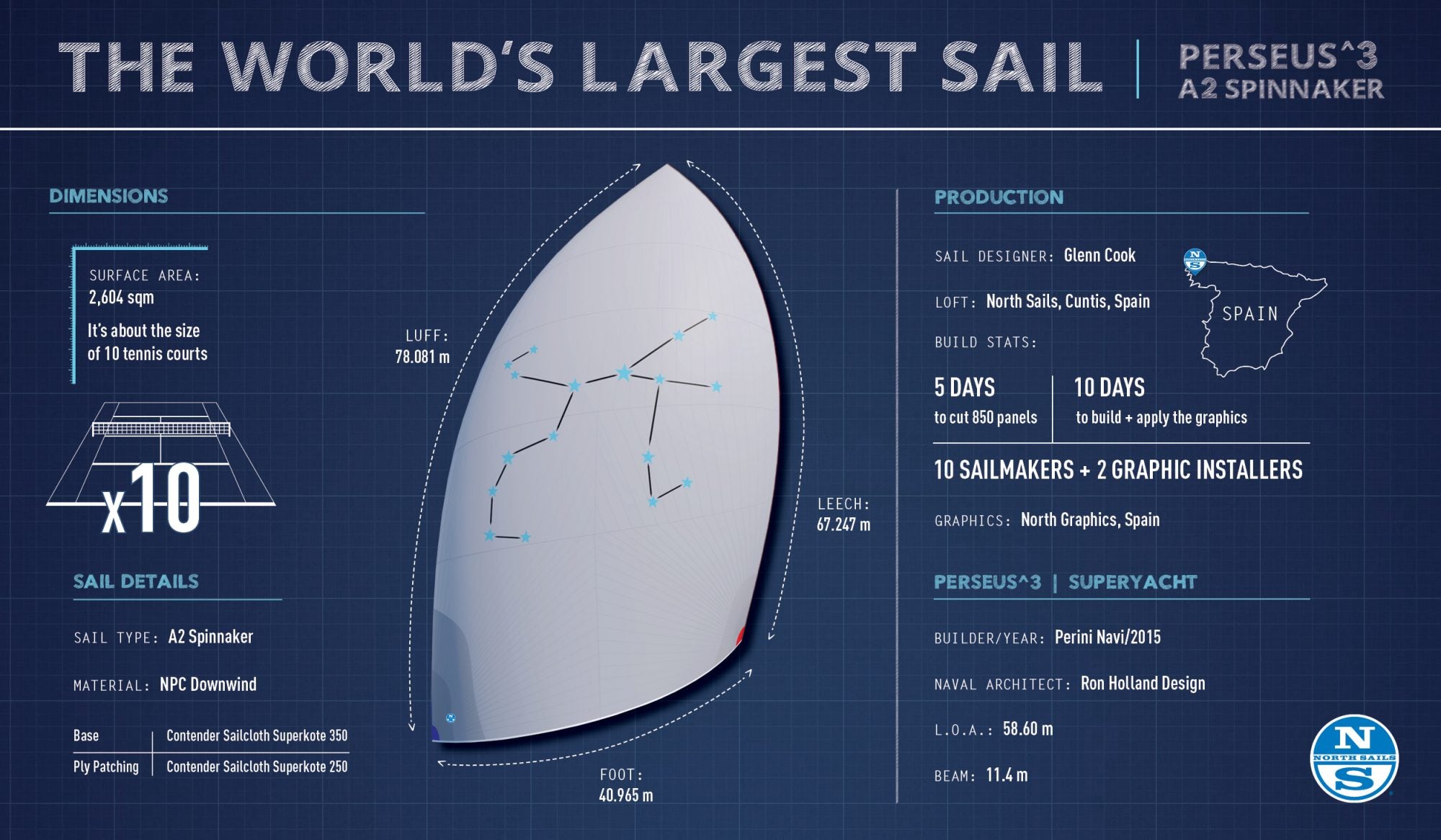
Det går åt många rullar duk till ett sådant här segel, och jämn kvalitet i produktionen är en nyckelfaktor för att seglet ska prestera på ett bra sätt utan lokala variationer. ”I dessa stora spinnakers är duken konstruerad på ett sätt som gör att den får lite inbyggd elasticitet. På så sätt leds inte stora chocklaster vidare genom riggen och ner till själva båten – seglet absorberar en del av kraften.
Det som skapade mest huvudbry var, kanske något förvånande, seglets specialbeställda grå kulör. ”Färgningen var det som tog längst tid, eftersom det inte är möjligt att färga så mycket material på en och samma gång. Maskinerna är helt enkelt inte så stora. Så du måste vara väldigt uppmärksam på blandningen av färgen och hur länge den får dränka in… men när du tittar på det färdiga seglet så ser du att vi har kommit väldigt nära! Och det underlättade väsentligt för Manuel när han skulle sätta samman själva seglet.
Manuel Lastra och North-loftet i Cuntis i norra Spanien var sista delen i detta stora pussel. ”Det tog ungefär åtta veckor innan vi fick allt material”, säger Lastra över telefon, och berättar att de beställde 400 löpmeter extra duk, detta för att vara säkra på att kunna göra en bra färgmatchning i seglet.
Totalt fick han och hans team 3323 löpmeter nylonduk, fördelat på 48 rullar, skickat till sig, plus ytterligare 500 löpmeter av den tunnare Supercote 250-duken. Med 3500 kvadratmeter duk fördelat på tre stora golvytor kunde Lastras team steg för sten montera ihop de olika sektionerna. För att få plats på skärbordet gjordes seglets undre del av fyra sektioner, istället för som brukligt två. ”Det tog fem dagar för två personer att skära ut våderna”, säger Lastra. När det var färdigt sorterades de 850 våderna i olika grupper och monterades ihop i sektioner. Därefter gick de genom symaskinerna.”
De olika sektionerna syddes ihop separat. Sedan monterades de ihop och hornförstärkningarna sattes på plats. ”Det tog tio dagar för tio personer. Parallellt jobbade två personer med det grafiska mönstret.”
”När seglet var färdigt fick det torka i fyra dagar innan det veks ihop och skickades till Antigua.”
Och det var på den närliggande karibiska ön St Barth som vi fick tag på designern Cook just som han höll på med sina segeltester.
”Jag är här nere den här veckan och seglar St Barths Bucket Regatta med dem. Det krävdes 16 personer för att packa upp seglet och montera det i spinnakerstrumpan.”
Seglet väger in på 550 kilo. Försökte han lyfta det?
”Det kan vi inte!” skrattar han. ”Vi använder vinscharna ombord. Vi kan släpa det, men det krävs tio till femton personer för att rubba det.
”Det är stort.”