3Di AND PANELED SAILS: HOW IT’S MADE IS WHY IT’S DIFFERENT
Sailboat sails fall into two main categories: 3Di sails (sails built on a 3D mold) and paneled sails (sails built on a flat surface).

North Sails expert Gautier Sergent explains the differences
While the 3D mold vs. 2D table construction is a big difference, that’s not the only way 3Di sails are fundamentally different from paneled sails. We’ll walk you through those elements so you can make the best choice for your next sail.
How Does the 3Di Sail Construction Make it a Better Sail?
We’ll answer this and the question “what is a North 3Di sail?” by talking about the materials and construction of a 3Di sail.
3Di Sail Materials
A 3Di sail is made of fiber and resin (glue) just like traditional sails. But it’s how North uses those materials that makes 3Di sails superior.
3Di Sail Structure
The fiber in a 3Di sail is made of spread filament tapes. The tapes begin as spools of fiber – same as all other sailmaking methods. But then North runs those spools through a machine that separates the fibers into filaments (hence the term “spread filament”), their original form. The hair-thin filaments are run through a bath of thermoset resin (we’ll get there in a minute) and then laid side by side in a single layer to form a tape. These 3Di tapes make up about 70% of the 3Di sail’s structure.
The tape material depends on the boat, sailing style, and performance goals. You’ll recognize the options: polyester, aramid, Dyneema, and carbon. But remember: it’s not what fiber materials are used, but the way North Sails applies those fibers that makes the difference.

Why no Mylar in 3Di?
Mylar, a popular sail material, is conspicuously absent from 3Di sails. In fact it is the weak link in other sails, string sails included. Because 3Di sails have 0% Mylar, there is a 0% chance a 3Di sail will delaminate.
3Di Glue: Thermoset Resin
The glue in a 3Di sail is thermoset resin, and it makes up 30% of the 3Di’s sail structure. Thermoset resin is a two-part adhesive that cures via a chemical reaction when heat and vacuum pressure are applied. Once cured, this resin is unchanged by heat, moisture, or UV rays – perfect for sails made to live in extreme conditions.
3Di Sail Construction
First, a North Sails designer determines the layout and details of a particular 3Di sail – size, shape, reef points, batten pockets, etc. Once the spread filament tapes are laid, they are placed on top of the mold and the sail is formed into its designed shape. Heat is then applied once the mold is vacuum sealed, to cure the thermoset resin. The completed product is a seamless composite airfoil. The consolidated composite then sits for 7-10 days on the curing floor. After curing, sails move onto finishing, where hardware, decals, and patches are added.
Overall Benefits of 3Di Sails
Due to the unique sail construction of 3Di, the sail does not distort under high loads and the spread filament tape layers provide increased longevity and minimize stretch, which resists damage from UV, chafe, abrasion and flex. 3Di sails last longer than any paneled sail on the market. And unlike mylar, 3Di sails will not delaminate, ever.
How is a Paneled Sail Different than a 3Di Sail?
Anything that’s not 3Di is a paneled sail. Paneled sails are put together on a flat 2D surface and shaped through broad seaming; the edges of each panel are tapered to be narrower at the edges than in the middle and then seamed to the next panel, creating depth.
Paneled sails include everything from a woven Dacron sail to a string sail made from materials like carbon and Mylar.
To understand more about the difference between 3Di and paneled sails, let’s dive into the different types – string laminates, laminate sailcloth, and woven polyester – and their limitations.

Woven Polyester Sails Compared to 3Di
To make traditional woven polyester sails, commonly known as dacron sails, we first make cloth by weaving spools of fiber into flat material. The material is laid out in either a tri-radial or cross-cut pattern. As part of our NPC family of dacron paneled sails, North has proprietary polyester cloth for each cut: Radian for tri-radial construction, and NorDac Fill for cross-cut. The pattern pieces are joined by glue and stitching.
While dacron sails are both durable and affordable, 3Di sails will have better performance and a longer competitive lifespan. Dacron sails are durable, but they will eventually show signs of stretching, chafe, and UV degradation.
Laminated Sails Compared to 3Di
Paneled sails made of laminate materials start with a film or taffeta layer. The laminate covers any gaps between the load-carrying fibers, which can be Dyneema, aramid, carbon, or a mix. Thermoset resin or stitching attaches the laminate panels. Paneled laminate sails by North are called NPL and suit everything from club racers to Superyachts.
Laminated sails don’t have the same load-carrying strength as 3Di sails because the fibers stop and start at each seam. To combat this structural discontinuity, designers specify fabrics that will best match a sail’s loads and align the fiber orientation with the load path of the sail. North makes laminated sails only in a radial design, to minimize horizontal seams and protect high load areas like the head and clew.
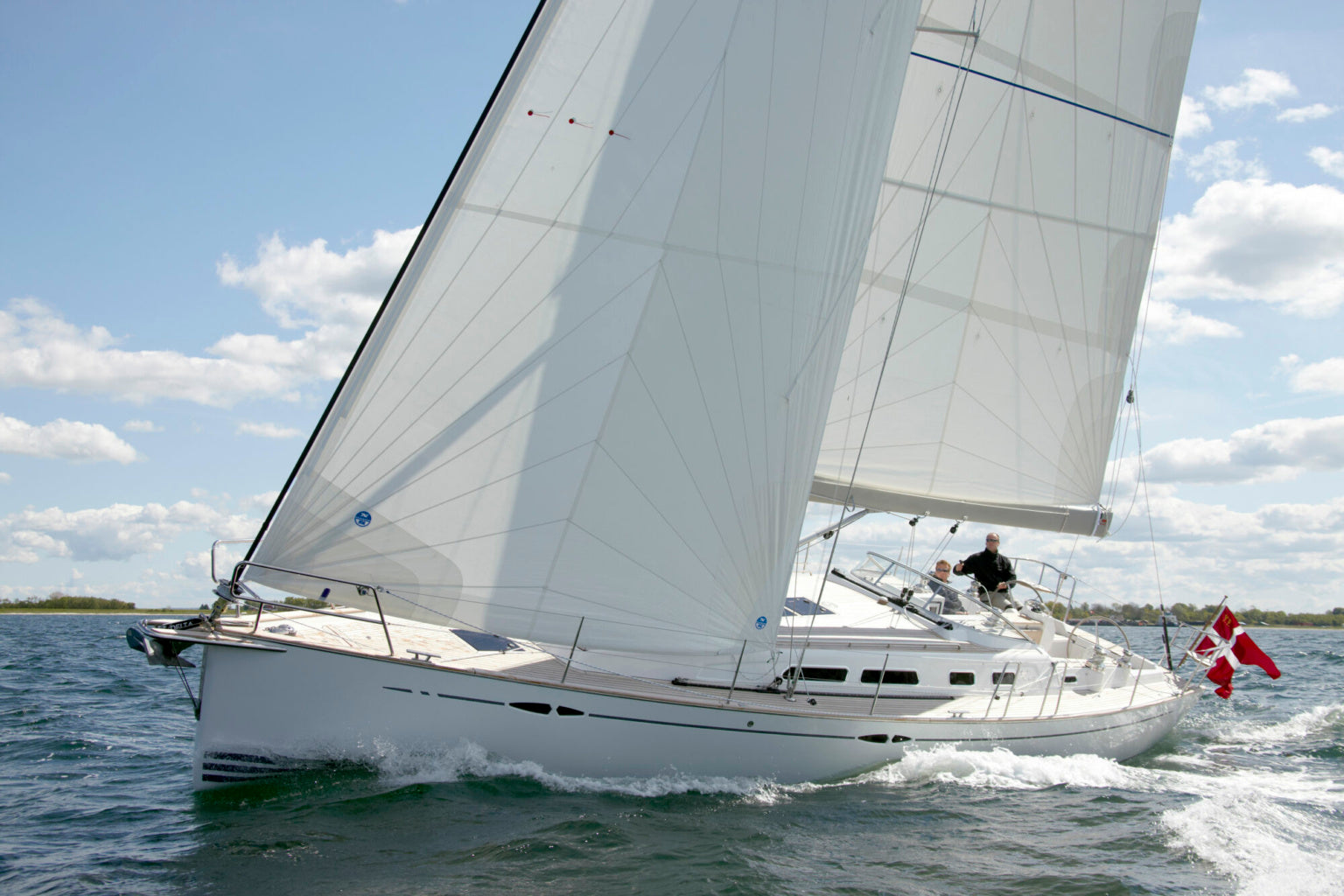
String Sails Compared to 3Di
String sails date back to the 1995 America’s Cup, when several teams used a new North design of carbon fiber sandwiched between Mylar. You know these as North 3DL sails. We built more than 70,000 of them. But in 2018, we shifted all 3DL production over to 3Di. Here’s why.
String sails are made from twisted yarn bundles sandwiched between Mylar and thermoplastic glue. The bundled yarns results in overlaps and voids between yarns and Mylar. Unlike thermoset resin, thermoplastic glue softens with heat. This makes a string sail more likely to break down in sun and moisture, or if you leave the sail in a hot environment – a parked car, for example. Paneled laminates and string sails have fiber discontinuity at the seams, which leads to stretching and shorter lifespan.
Are string sails comparable to 3Di sails?
The combination of the fiber, glue and seams of a string sail results in a weaker, stretchier, heavier sail structure compared to 3Di. String sails lose their shape faster, which means you’ll have to buy replacement sails more frequently. That’s why North stopped making 3DL and switched to 3Di: because 3Di is a much better product. Other sailmakers are still refining the manufacturing process of string sails, but working with a paneled construction method is limiting their potential progress.
3Di: Smoother, Stronger, More Durable Sails
Understanding the differences between the three current sail manufacturing techniques makes it easy to see why 3Di is the best alternative. With customizable options that fit everyone’s needs – from Superyachts to cruisers to club racers – the 3Di revolution has truly brought sailmaking into the 21st century.