LARGEST SAIL EVER BUILT, PERSEUS^3 A2
MAKING THE WORLD’S LARGEST SAIL
Meet the Designer, Builder, and Cloth Supplier of the Superyacht Perseus^3’s New Spinnaker, a Sail the Size of 10 Tennis Courts

“It’s substantially bigger than anything else out there,” says Glenn Cook in a typically measured fashion. The North Sails superyacht sail designer is calling from St Barth, where he’s testing the sail out for the first time, a process he says is both “nerve-racking” and “the best part of the job.”
Because to bring this 2,604 sqm A2 sail to life, it’s taken a lot of people, time, and resources.
In fact, it’s taken a design team in the US, an eight-week custom order from Contender Sailcloth and a team of 10 sailmakers and 2 graphic installers working over 15 days to build this sail.
“The boat was specifically looking for a target area from a rating perspective,” explains Cook. “So the design was driven by that. And because Perseus^3 is a huge boat (her length overall is 58.60m), you can’t turn very quickly and trimming adjustments are also slow, so we looked to make a sail that had a very stable flying shape. Plus the sail has to work across a variety of conditions. The design is more forgiving than you would do on a smaller sail.”
Handling issues drove the design, too: the luff is so long that it can drop into the water when gybing. “We developed a system above the tack to collect the sail and keep it clear of the water during a gybe.”
With no other sail of that size or real benchmark, the chosen base material is a Contender Sailcloth Superkote 350 – the top of their offering – and the ply patching a Superkote 250 to keep some weight off.
“These boats are huge, the loads that are involved are pretty exceptional,” adds cloth supplier Duncan Skinner, President of Contender Sailcloth USA. “We go from a fabric that weighs 32 grams per square meter up to something that weighs 150 grams for the Superkote 350 in this kite. As the weight goes up, the strength goes up and that’s what you need in a sail this size.
“The fiber selection comes first – it’s high-tenacity Nylon. Second, constructions, ie. how many yarns we weave in each direction. Once the fabric is woven, the finishing comes in – that’s the real trick. You have to dye the product first, then finish it. We finish it with a coating process that gives stability and zero porosity to the fabric. A well-proven chemical process that makes fabrics that withstand the kind of loads you see on these giant boats.”
Skinner smiles. “This thing is so big!”
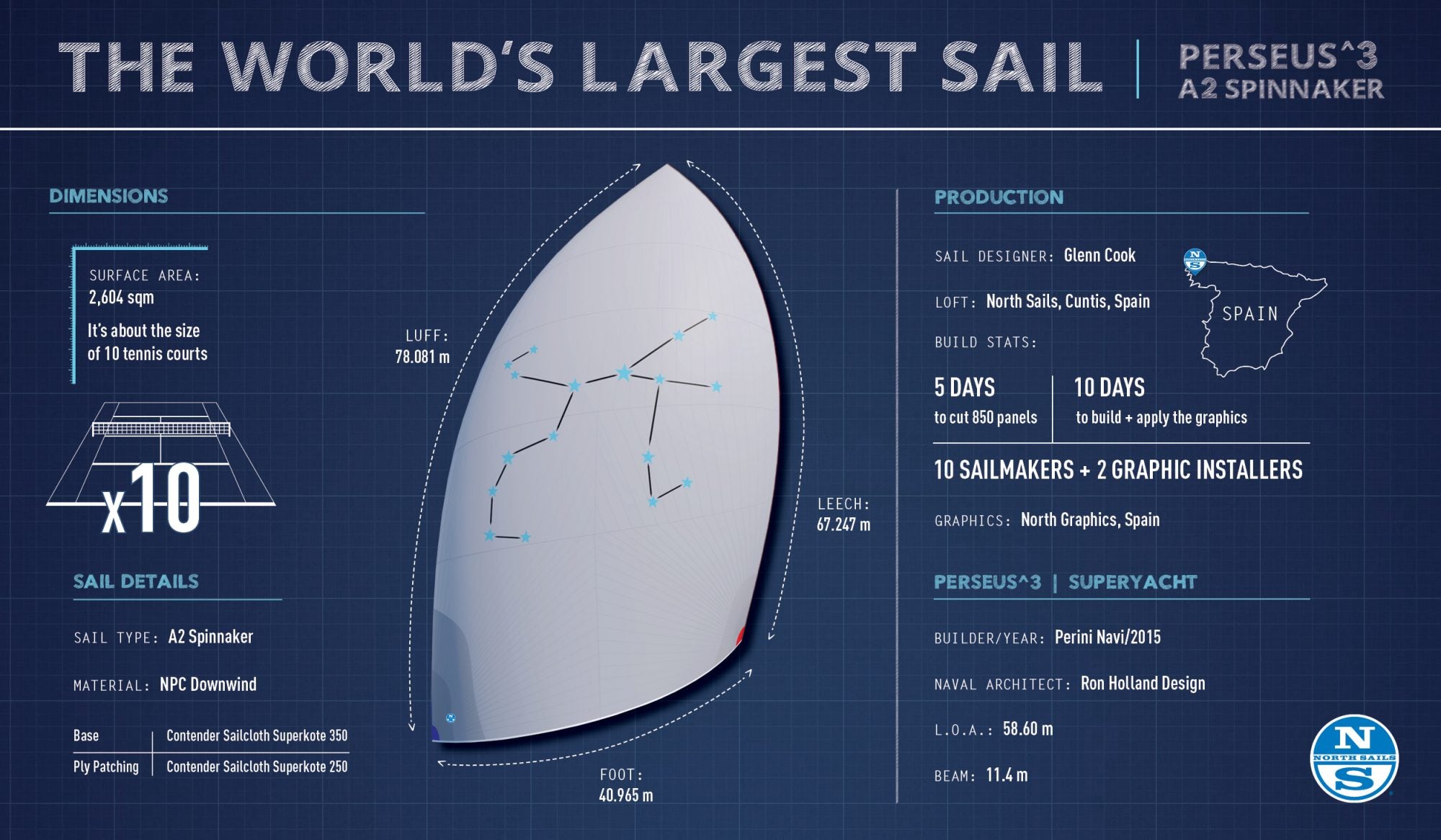
Producing a consistent finish throughout is key to ensure the sail’s uniform performance. “On these big kites, the fabric is specifically engineered so that there is a little bit of elasticity built into it. That way, big shock loads don’t run back through the rigging and the boat itself – the kite absorbs a little bit of it.”
Surprisingly though, it’s the sail’s custom grey color that caused the most headache. “The coloring took us the longest because you can’t take that amount of material and dye it all at the same time. The machines just aren’t that big. You have to pay a lot of attention to the dye formulation and to the timing… and when you look at the kite, it’s pretty damn close! That was also very good on Manolo’s part when assembling the sail.”
Manolo Lastra’s loft in Northern Spain was the last part of this gigantic puzzle.
“It took about eight weeks to receive the material,” says Lastra on the phone, explaining how they ordered around 400 linear meters extra to get the panel color right.
In total, his team received 3,323 linear meters of material divided into 48 rolls, used 3100, plus another 500 meters of the Superkote 250. With 3,500 sqm over three floors, Lastra’s team assembled the different sections step by step. And to fit the cutting tables, the sail has four sections across its foot, where most sails have two.
“Two people were cutting for five days,” says Lastra. “Once cut, the 850 panels were sorted by groups and sent to production to be assembled by sections. Then they went through the sewing machines.”
The parts were sewn separately before being put together. “That’s when we started adding the plies in the corners,” he adds. “That took 10 people and 10 days. Two more people were working on the graphics in parallel.
“Once the sail and graphics were done, it dried for four days, got folded, and shipped to Antigua.”
And it’s on the neighboring Caribbean Island of St Barth that we find Cook testing it out.
“I’m down here sailing with them for the St Barths Bucket this week. It took probably 16 people two hours to unfold the sail and put it into the spinnaker sock.”
At 550 kilos, did he try lifting it?
“We can’t!” he laughs. “We use winches on the boat. We can drag it, but that still takes 10, 15 people to move it.
“It’s big.”