POLISH TRIFECTA OF TRADES: SAILMAKERS
POLISH TRIFECTA OF TRADES: SAILMAKERS
Women Who Play Key Roles Within The Leading Sailmaking Brand

At one of two North Sails production sites in the United States, three female sailmakers are devoting their highly trained eyes to building the best products for our clients. Regina, Margaret, and Basha all moved from Poland to Milford, CT to raise their children and make a career out of their lifelong love of sewing. Thirty-plus years later, they continue to form a “Polish trifecta of trades,” specializing in prefabrication, finishing, and assembly. They’ve even helped with larger projects like the Volvo Ocean Race and the America’s Cup.
“The expertise that Regina, Margaret, and Basha bring to our company is enormous,” says Steve Gruver, Floor Supervisor. “They are outstanding employees and a delight to work with. They enjoy working hard and do an excellent job with any project they are assigned. Whether it’s prefabrication or in the pits perfecting larger-scale projects, we can trust they will go above and beyond. We are very lucky to have them here- part of our Milford family.”
-Steve Gruver, Floor Supervisor
Regina Golimsek was the first to start working at North Sails in 1980. Trained to make clothing, she says at first that sailmaking was a lot harder. “The material is much stiffer, not like a dress. My first time I couldn’t sew in a straight line, and I almost quit! They told me to take my time, and I’d get used to working with the materials. They were right; I’m still here.” 2019 marks her 38th year at North Sails.

Another challenge was learning the sailing language to understand what each project required. “At our old facility in Stratford, I remember having to work with a furling sail and we had half of it inside, and the rest went out the door, where we tied it to the van to pull it tight. There we could get it furled up, and I could see how it worked. It was interesting to see the finished product, how it worked, how it should look, and also very funny to see everyone looking at us like we were crazy.”
Since the larger loft as built, there’s enough space to work inside. “Having more space to be able to take on the larger scale projects was what everyone was excited about. Providing the right tools allowed our staff to be the best it could be.”
Today you’ll find Regina in prefabrication, where she collects the correct parts for each sail— choosing rings, tapes, cords, cutting reinforcements for headboards, clews, batten pockets, snaps, and covers. She takes pride to make sure every box is checked, and each tack, clew, and headboard has the correct fittings and proper reinforcements.

“I like this job because it allows me to use my brain. Creating something, making things fit together; I get to figure out how to do it and make it perfect.”
Margaret Skakacz also left Poland to raise her family and start her career. “Raising a child and balancing work is hard. Childcare is not affordable. North Sails made it possible for me to work and take care of my children, and I’ve been very successful because of it.”

Before moving from Poland in the early ’80s, she attended school for physical therapy and prosthetics. Though her hobby was sewing and making clothing, she never thought she would make sails. 31 years later, she’s the leader in Quality Control at the Milford loft. “I make sure everything is right before it leaves the building,” she says. “I check every detail, make sure each sail has exactly what was requested. I make sure it looks good. It’s satisfying. Seeing a project through from start to finish is what I like the most. I can say ‘I did that’ and it looks good—like, America’s Cup good.”
Margaret gained a more technical understanding of sailmaking when she spent three years helping build 3DL string sails in Minden, Nevada. She worked alongside mentors like Jeff and Dan Neri to develop the original 3Di finishing standards. She says Mark Taylor, a North designer, was also very helpful. “To make the best sails, for certain projects they’ll bring in the best from all over the world to get the job done,”she says. Margaret also thanks Lucio Bolognani, who focuses on superyachts and specializes in hardware. “He came up with new ideas for bigger sails, which has made an impact on how we manufacture them today.”
“3D sails are much harder to work with,” said Margaret. “They come out from the factory in one piece, and are very stiff. It can be hard to work them through the machines, especially when the headboards, tacks, and clews are reinforced with webbing and much thicker. Reefs are by far the hardest since there are no sections to connect, it leaves no room for error.”
Margaret likes seaming panels the best. “Each sail order comes with a blueprint, and you see what the sail needs to look like finished. All cut into sections, and each section is numbered. How wide the seam allowance is, what thread weight to use, and what color to stitch with are all significant details. On each ticket, the details are listed in Blue Book codes, everything you’d need to know to make sails. The main goal? To make every sail look seamless.”

She also worked with PUMA in the Volvo Ocean Race and for one of Dennis Conner’s America’s Cup teams. “Margaret is one of our master sailmakers,” North Sails CEO Dan Neri says. “She has built thousands of North Sails, ranging from One Design to Superyachts, and nylon to 3Di. I had the chance to work with her for a few years in Minden. She always had a better, simpler idea.”
“What I like about this job is that it’s challenging,” Margaret says;
“New improvements processes, new designs—that’s what makes it hard but fun at the same time. We have a great crew here in Milford; we’re perfectionists. You know you’ve got a good thing going when they want America’s Cup sails made here.”
Part three of the Polish trifecta is Barbara “Basha” Balikowsky, who has been assembling sails on the North Sails floor for 30 years. “I like this job because it is always interesting,” Basha says. “There is always something to learn.”

Most of the sails that get made in Milford are custom, so no two projects are the same. The most critical part about sailmaking, explains Basha, is following directions. “Even if you think you’ve seen it before, you can’t skip it. I read the ticket two times first, always. You cannot repair a 3Di sail like you would a paneled sail. With 3D it’s all one piece—which means no mistakes.
“The North Sails logo stands for quality,” she continues, “and that’s what you get. Seeing the products from start to finish is what makes us proud to work for a company like this, and has allowed us to contribute what expertise we have. Even if it’s just sewing, we are proud of each sail that goes out the door and know our customers are getting the best sails.”
“I love this job,” she adds. “It’s like a big family. It makes it worth coming to work. I may not be able to sail, but I can run a sewing machine and make a great product for sailors. Not many sailors can do that.”
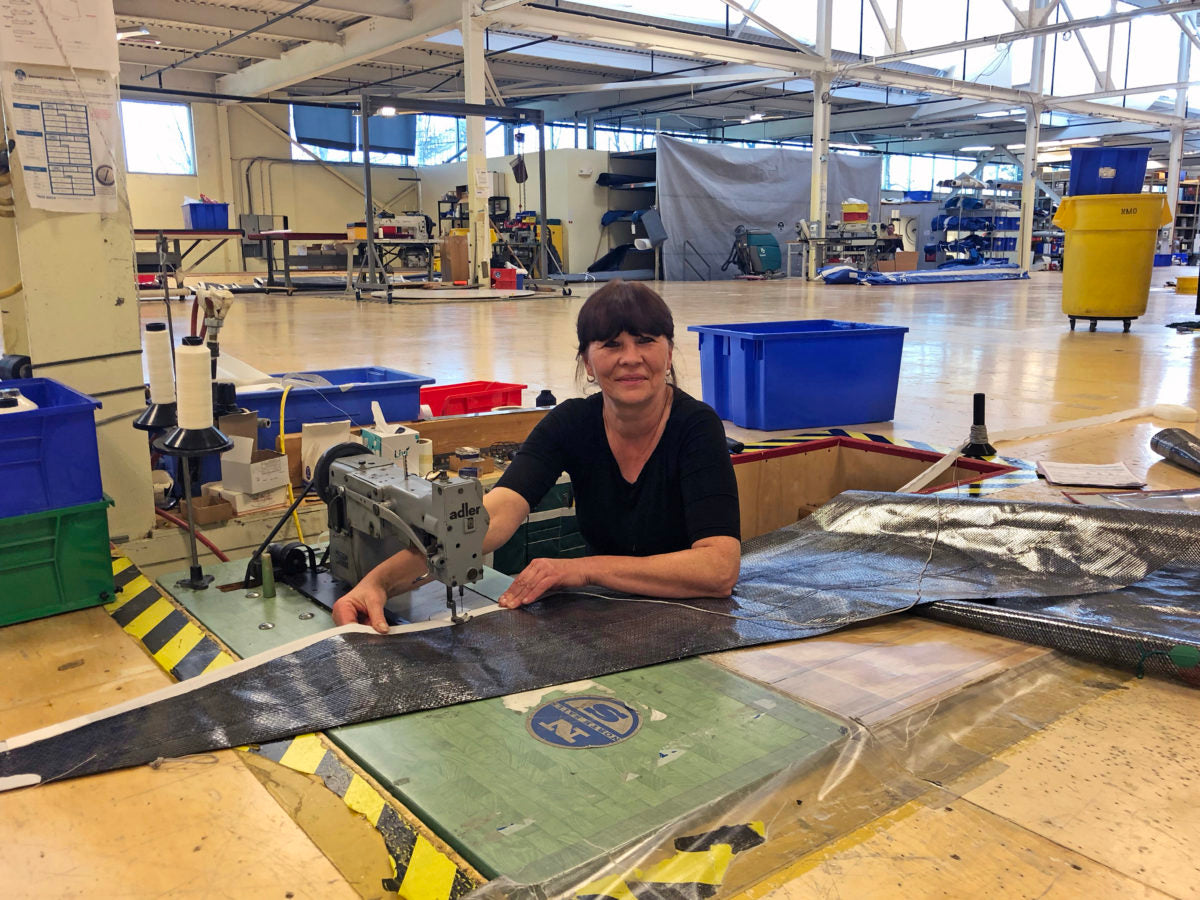