TECH JOURNAL: NORTH 3Di FOR THE 49ER AND 49ER FX CLASSES
TECH JOURNAL: NORTH 3Di FOR THE 49er & 49erFX CLASSES
After an intense bid process that included rigorous sail testing, the class unanimously chose to adopt 3Di, the most modern sailmaking technology
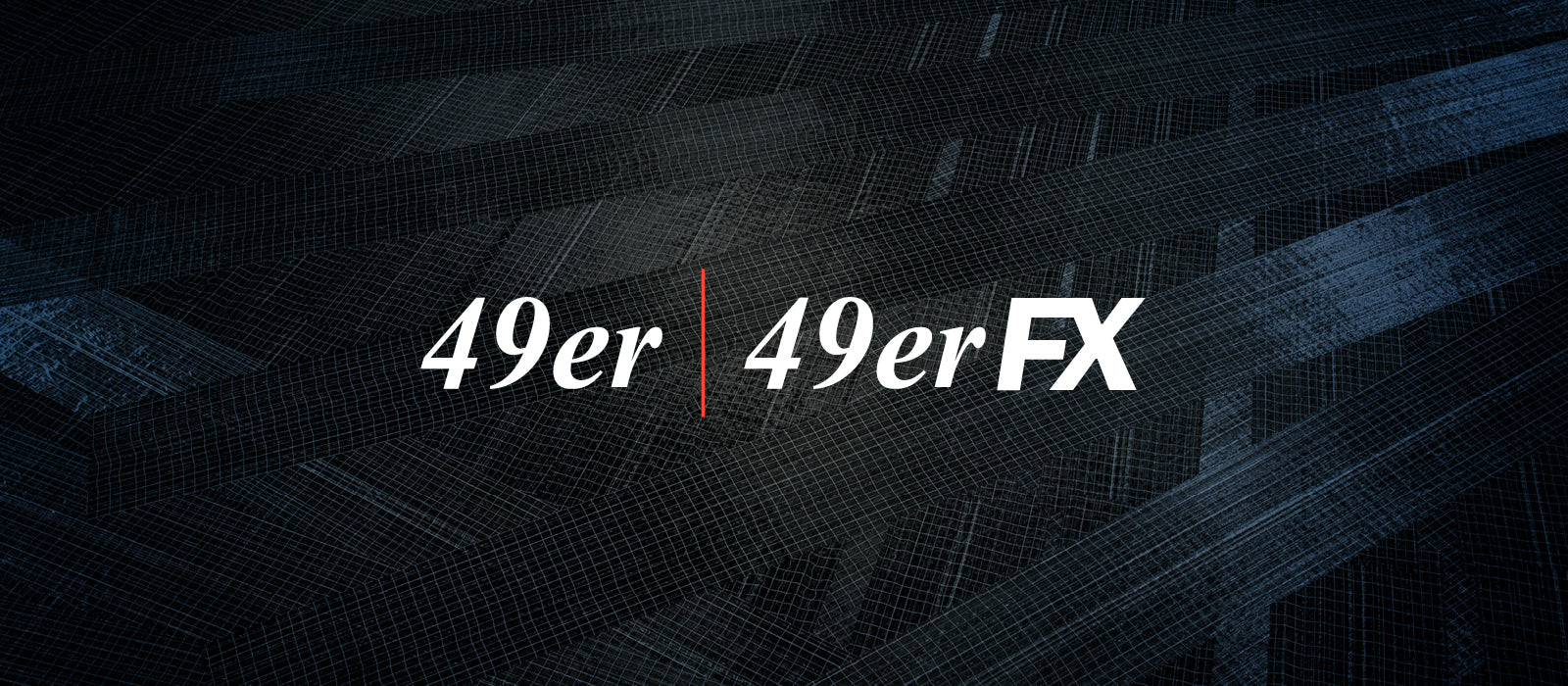
When North Sails was asked by the 49er and 49erFX classes to propose an update to their current sails, the first step was to collect accurate data about how they were performing and what could be improved. We reached out to Julian Bethwaite, John Clinton, Blair Tuke and Peter Burling, as well as many others who are involved with the class. The feedback was overwhelmingly in favor of better consistency in the sails and more longevity. Our goals quickly became very clear.
North Sails takes a scientific approach to sailmaking. The North Design Suite is a powerful set of proprietary software that allows our designers to model simulations, test hypotheses and eventually, arrive at an optimized solution for the engine above deck. This data-driven approach was visibly on display at the 36th America’s Cup, where North designers were embedded with Emirates Team New Zealand, Luna Rossa, and INEOS Team UK.
For the 49er project, it was months of design work and on-the-water testing to conclude that the best sails for the job were 3Di upwind sails. The process that we used to get there is described below.
Modeling & Materials
Our discovery for the 49er project began with an eagerness to fully understand the boats and the existing sails. Consistency of both manufacturing and shape, along with longevity, were identified as key areas for improvement. We learned that sailors were buying up to seven inventory sets just to find two that are consistent, so we set a goal to build a set of sails that would be consistent and competitive for up to three regattas. That would reduce sailor aggravation, drastically improve consistency, and also reduce overall inventory costs.

Modeling:
First, we built a virtual model in the North Design Suite that included the shrouds, mast and sails and made it possible to change the tuning for different wind ranges. From there, sail designers Mike Marshall and Mickey Ickert used a combination of five NDS tools (Desman, Spiral, Warps, Flow and Membrain) to run simulations and accurately predict the performance and shape of the current sails—as well as an initial recommendation for new sails.
Material Choice:
Once we could accurately predict sail performance and flying shape, we A/B tested two material options that could achieve the right shapes: a paneled laminate ; and North 3Di. The paneled cloth matched the current class specs while the North-manufactured sailcloth provided improved consistency in both cloth quality and construction. Made using the purpose-built EXact x-ply machine, the sail cloth was produced using a very precise gravure process to ensure perfectly measured adhesive coating; even glue distribution (and less glue overall) would reduce weight without sacrificing strength.
While our paneled laminate sails would’ve been a small step forward, we were certain that 3Di would be a much more significant improvement in our stated goals: improving both repeatability and longevity.
3Di would also be vastly different from the current class sail material and construction, so we knew it was important to prove that it would be dramatically better.
Fine-Tuning:
With our materials chosen, we fine-tuned our model to match the cloth. For the paneled designs, the goal was to optimize the shape through broad seaming and luff curves. For the 3Di sails, we leaned on WARPS™ for a layout that would maximize durability. We looked at both element strain and yarn strain in the model, which we can control well with 3Di.
Why 3Di tested better than paneled sails
When modeling, strain maps highlight “hot-spots:” areas where the element strain (a measure of the movement in the cloth) is too high relative to yarn strain (a measure of the tensions in the yarns). Small tweaks in tape layout may help one map but hurt the other, so we run the model until we strike the optimal balance. The strains don’t have to be brought down to zero; they just have to match each other.
Tension is the enemy of sail shape, and the key to designing a versatile, predictable sail is to align that tension with the direction of movement. Like an elastic, the more a sail is stretched against the yarn path, the less likely it is to come back to its intended shape. By optimizing tape materials and orientations, 3Di allows us to minimize distortion under load, which will help with consistency, performance, and longevity.
On paneled sails, the yarn strain is high but the element strain is low—especially in the main. That means the sails are pliable, but they will change shape over time.

When compared to the 3Di sails, the original 49er main showed the element strain to be high in the upper third of the sail. Based on our experiences, this led us to add more bias support and use tapes at different angles from our standard load path layout. That settled the element strain map and made it more consistent with the yarn strain map.
On the paneled main and jib, the map showed high yarn strain up the luff of both sails. There wasn’t much we could do about that in the paneled sails, but in the 3Di sail we added a Helix structured luff group to both main and jib. That settled the yarn strain map and brought it more in line with the element strain map.
A 3Di main that uses a custom-engineered layout and a 3Di jib that uses the standard load path layout best matched the maps of the element and yarn strains. And by settling the luff loads, the Helix luff structure would make the cunningham and halyard more effective.
No detail is too small
After developing prototype designs that fulfilled our primary goals, it was time to look at the small but important details that contribute to overall performance.
The tack flap connection in the main was noted as an area of high load and distortion since it is the point of convergence for the two tack flaps and the bottom batten. We reinforced it in the paneled sails, and then re-thought it in the 3Di sails to be all one piece. That single structure will transfer cunningham load to the head of the sail, eliminating a high failure and wear point.
Next, we built prototype sails in both paneled and 3Di, and we invited several experts to go sailing.
Sail Testing
With the help of 18’ Skiff expert Matt Steven, the prototypes were put to work by the top New Zealand 49er teams. After several on the water testing sessions, the simulations we’d run in the North Design Suite were validated.
With the help of 18’ Skiff expert Matt Steven, the prototypes were put to work by the top New Zealand 49er teams. After several on the water testing sessions, the simulations we’d run in the North Design Suite were validated.
We were very pleased with the performance of all the new sails against the current designs. Both paneled and 3Di held their shapes and were more consistent than the class standard, though as we predicted the 3Di sails were smoother, more consistent, and held their shapes better. Shortly after our testing sessions, our recommendation that the class adopt 3Di was accepted.
For both training and regattas leading up to the 2024 Olympics, 49er and FX sailors now have a much better option for sails: 3Di mains and jibs. They will be built with the same sail technology used to make identical sails for one design classes such as the Volvo 65s, AC50s, Moth and Melges 20; a constant and replicable taping and mold, followed by a consistent layout and finishing team. We met our project goals in order to help you meet yours—another example of the North Sails scientific approach to sailmaking.
Testimonials: Longevity
18ft Skiff – In four years, David McDiarmid’s Honda Racing earned the JJ titles, widely recognized as the 18’ Skiff’s World Championship. The team accomplished this with one set of 3Di sails. Between training and races, these sails saw thousands of hours on the water.

Moth – The class has almost entirely switched to 3Di sail, which like the 49er, is a full battened mainsail with very high loads. Most of the sailors buy one sail a year and use it for all of their major events. Comparatively, sailors would go through 2-3 paneled sails per in advance of each major event. Tom Slingsby says: “The North 3Di Moth sail has a longer durability than any sail on the market I had previously used, and any sail currently on the market. If I was heading into a world title this year, I would have no issue using the sail I used to win the 2019 World Championship. The life of the sail is outstanding.”
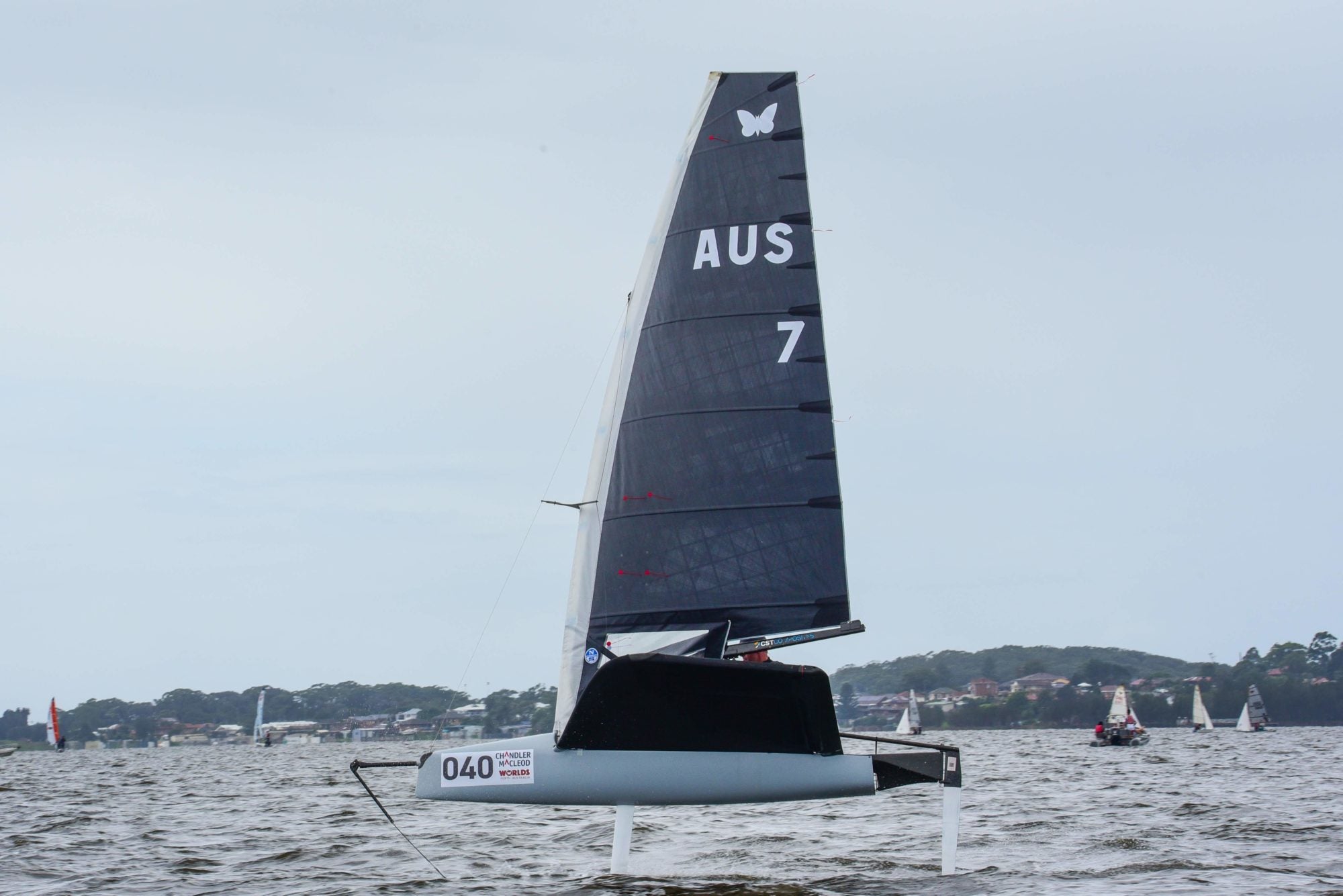
Around the World Ocean Racing – North 3Di has been tested through hundreds of thousand hours and offshore miles. Whether the one design Volvo 65, the latest generation IMOCA or the awe-inspiring Ultim trimarans, 3Di is made to outlast the adventure. For example, the sails used by Thomas Coville in his 2016 around the world record were used for a year and a half of training and practice leading up to his attempt. He reported no sail failures in the 42 day trip around the world.