SPAN SQUARED
SPAN SQUARED
What Does It Mean When Wings Create Lift?
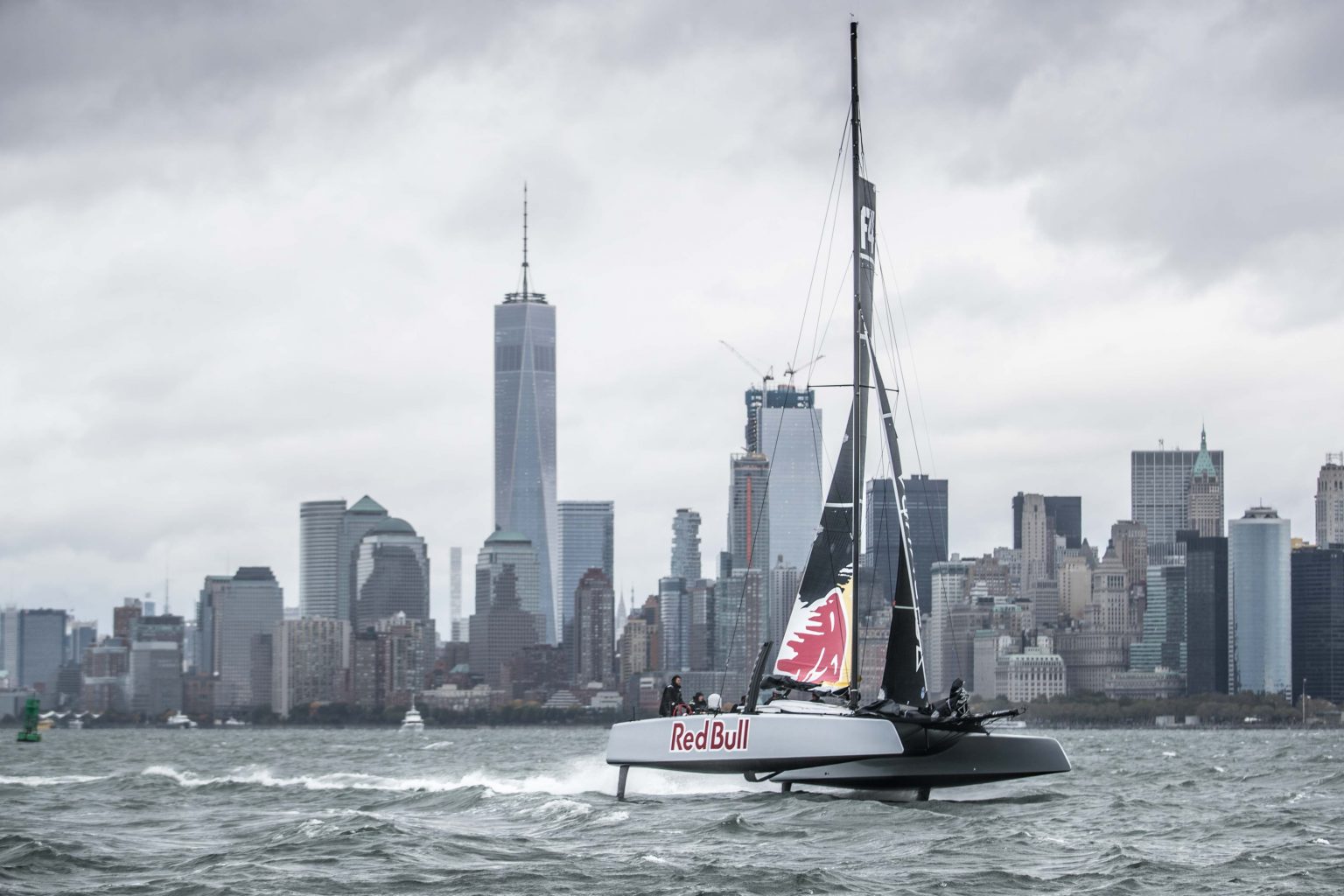
When a wing (like a sail or a keel or centerboard) produces lift, an accompanying drag force is generated called induced drag. This is related to pressure that is lost around the wingtip and the formation of vorticity. A wing is considered to be more efficient if it produces lift with less induced drag.
Common understanding is that induced drag is lower for higher aspect ratio wings. This is apparent by reviewing the standard equation used to calculate induced drag which contains the term aspect ratio. The problem with this equation is that it defines the value of the induced drag coefficient using the lift coefficient, which is not necessarily constant depending on how aspect ratio is changed.
The equation is useful in situations where the wing area is the same, such as these two wings. Notice that while they have the same area, they have different spans.
A useful definition is to relate aspect ratio to the span and area rather than to the span and chord. This is particularly handy
for tapered wings.
Lift coefficient and drag coefficient are non-dimensional terms that indicate how hard a wing is working regardless of speed or size. Dynamic pressure, which depends on the velocity squared, and area are divided into the lift and drag forces to define these coefficients. As area changes, the coefficients required to generate the same force will change proportionally.
Since the equation for induced drag coefficient relies on the lift coefficient, it is susceptible to changes in lift coefficient that can occur as the aspect ratio changes. For a fixed amount of lift (force, not coefficient), if the aspect ratio is increased by making the span longer while keeping the chord length the same, which adds area, the lift coefficient will be decreased due to the greater area. If the aspect ratio is increased by keeping the span the same length and decreasing the chord length, then the lift coefficient will be increased due to the smaller area. When aspect ratio and lift coefficient both change, it becomes more complicated to assess what the affect is on induced drag.
There is a simpler way to understand how induced drag is affected. By performing some appropriate substitutions in the induced drag equation and simplifying the terms, we define the induced drag force rather than the induced drag coefficient.
The result is that this equation shows that induced drag is proportional to the lift force (not coefficient) squared divided by the span squared. This means that span, not aspect ratio, is the determining factor for the efficiency of a wing. Area and chord do not appear in the final equation and do not impact induced drag. They do affect the viscous (frictional) drag, though.
Unlike the original induced drag coefficient equation, which implies that induced drag is dependent on aspect ratio (but only when the area is kept constant, meaning that as aspect ratio is changed, chord and span are modified to maintain the same area) this equation demonstrates that the induced drag force is really dependent on the amount of lift squared and the span squared. This reveals that the reduction in induced drag in the previous span comparison example is really due to the increase in span. The power of the squared term is significant because, for example, if span is doubled, the induced drag is decreased by a factor of four. Even a 10% increase in span results in nearly 20% less induced drag.
Understanding that induced drag is inversely proportional to span squared has value to improving sailing performance.
A common misconception is that a centerboard or keel with shorter chord but the same span is more efficient because it has higher aspect ratio. When we recognize that when span is the same, induced drag is therefore the same, we can properly attribute any performance differences experienced to the difference in area. These differences relate to the viscous drag instead, which is the friction of the fluid flowing over the surface and is dependent on the area, and also to changes in angle of attack (leeway and apparent wind) that occur as area is changed.
An example of the affect of span on sails that is common for many one designs is that as speed increases, raking the rig aft has been found to be beneficial to performance. This can be explained through span squared.
After a boat has reached its righting moment limit (crew fully hiked or trapezing, or practical limit of heel for a keelboat) the amount of force that the sails produce cannot be increased any more (without causing excessive and detrimental heeling). In order for the boat to go any faster, the drag needs to be reduced. The longest edge of the sail is the leech, which as the rig is raked aft becomes more vertical and maximizes span. So, with the same lift being produced over a sail with greater span, the induced drag of the rig is reduced and the boat can sail faster. In the most extreme case, comparing an upright luff to an upright leech, the induced drag would be decreased by the ratio of the luff length divided by the leech length, squared.
Another benefit of raking the rig is that the clew becomes closer to the deck, and as the trailing edge approaches being sealed, there is less pressure lost around under the boom and the sail becomes more efficient. Span-wise change in pressure differential is what causes vorticity to be shed from the trailing edge. Increasing the distance between the vorticity shed from either end, or reducing the vorticity shed yield higher effective span, hence lower induced drag.
Since drag also contributes to heeling, a lower heeling force allows the total force on the sail to be increased up to the righting moment limit, further increasing the boat’s speed.
When the rig is raked aft to maximize span by making the leech more vertical, the height of the sail is slightly lowered becoming closer to the water where the wind velocity is lessened by friction with the water surface. While this is not a problem once the boat has reached the righting-moment- limited condition where de-powering (and drag reduction) becomes necessary, it might explain why it is not always advantageous to sail with the rig raked aft in lighter wind conditions when creating more sail force could be the overriding factor.
As the rake of the rig is changed the location of the sail’s force moves with it. This changes the loading required on the rudder in order to make the boat sail straight. While this may limit mast adjustment, the potential benefit creates incentive to discover how to set up the boat to take advantage of the lower induced drag of a more raked rig.
The concept of span squared can also be used to determine the optimum rudder load, either to define the reasonable extent of mast rake or to minimize the drag of the underwater foils for a fixed mast location. The keel (or centerboard) and rudder should both contribute to the boat’s side-force to counteract the sail’s side-force. Determining the appropriate load for each can produce significant performance improvements.
While there are some interactions between the two foils, a simple approach to determine the minimum induced drag is to treat each foil as isolated and sum the drag of each. The result with the least induced drag is that the foils should contribute to side-force proportionally to the ratio of their spans squared.
It is important to consider the span as twice the physical span of the keel or centerboard because it is sealed against the bottom of the hull, which acts as a reflection plane. This is because the pressure differential across the sealed foil is maintained at the hull intersection as if there were a reflected image of the keel protruding upward. A completely immersed rudder that is sealed under the hull can also be considered to have a reflected image that doubles its physical span, but a transom hung rudder that pierces the surface of the water would only be considered to have its physical span without a reflected image. This is because the water surface can deflect due to the pressures imposed on it by the surface piercing foil. As the water surface deflects, the pressure differential at the surface is degraded and the surface piercing rudder loses the benefit of a reflected image.
The difference in effective span between an immersed rudder and a transom-hung rudder indicates that most keelboats (with immersed rudders) should be sailed with more rudder load than most dinghies (with transom-hung rudders).
An additional factor is that as rudder load is increased through deflecting the rudder, the leeway angle of the boat is decreased. Decreased leeway has the additional benefit of a higher apparent wind angle and the opportunity to produce higher sail force. This makes it is very beneficial to deflect the rudder at least to the angle that produces minimum induced drag for the whole boat and gain low induced drag, a higher apparent wind angle and larger sail force, and less leeway, all of which contribute to better pointing. It could even be useful to sail with the rudder deflected somewhat beyond the loading that minimizes induced drag. The small additional increment in induced drag for a modest increase in rudder angle could be offset by further improved pointing ability.
A boat with a gybing centerboard or adjustable flap on the keel already has the capability to reduce leeway and improve the apparent wind angle and may not benefit as much from overloading the rudder as much as a boat with a fixed centerboard or keel.
Since sailing with the appropriate rudder load can have a significant affect, particularly in one-designs where there are limited opportunities for performance improvement, it is valuable to determine what the target rudder angle should be. Assessing the issues for a specific boat requires knowing the dimensions and loads. These can be analyzed to produce specific target settings or designs (if allowed).
Here is an example of how induced drag is minimized through optimizing the load sharing of the keel and rudder.
The total amount of side-force that the keel and rudder produces is kept constant but the amount of side-force that each contributes is varied. By ignoring the affect of each component on the other (a simplification that is more valid as the distance between them is large), the induced drag of the keel and rudder can be calculated separately and added together. In this example the keel span has been chosen to be four and the rudder span to be three. The units do not matter, since we are merely looking at the proportionality of the load. Assuming 100 total units of lift, induced drag is shown for several possible load distributions. Note that minimum induced drag occurs when the load is distributed proportionally to the ratio of the span of the keel and rudder, squared (for example 64/36 = 8/6 squared, and 88/12 is close to 8/3 squared).
The example is shown two ways: with an immersed, sealed rudder that benefits from a reflected image with twice the span, and with a transom-hung, surface piercing rudder that only has an effective span equal to its length. The lower induced drag with the longer effective span rudder is dramatic. But what is important to recognize is that the optimum load sharing distribution is quite different between the rudder styles.
While the longer acting rudder can take 36% of the side-force leaving 64% for the keel, the shorter acting rudder can only take 12% of the side-force leaving 88% for the keel. That causes the lowest possible induced drag value to be 37% higher in order to produce the same 100 units of side-force. Again, the units are artificial, as the constants dynamic pressure and pi have been left out of the equation so we can just look at proportional relationships. A similar amount of drag reduction could be expected for the same style rudder that was replaced with one that had twice the span.
Within the constraints of one-design rules, that type of change is usually not allowed, but there is still the potential to achieve a load sharing that yields the lowest possible induced drag for the configuration. The increases in induced drag as the proportions are varied away from the optimums are shown and give incentive to set the boat up to achieve loads that generate the lowest possible induced drag. Also evident is that being away from the optimum is more severe for the shorter span rudder configuration than for the longer span rudder configuration.
By applying the relationship of span squared, the target loads can be determined for a specific boat. The challenge then is to achieve those loads. This is accomplished through changing the mast position, either by moving the mast step or adjusting rake in order to establish the location of the sails’ force so that the boat will sail straight with the rudder deflected to the desired angle that minimizes the induced drag of the underwater foils. As the mast is shifted aft, the rudder load required to make the boat sail straight increases, and as the mast is shifted forward, the rudder load will decrease. Finding the optimum can have a noticeable affect on performance. The goal is to efficiently use the spans of both foils.
Often, a boat has the mast too upright and hence, is not properly loading the rudder. Raking the mast back can cause the rudder load to increase, which decreases the underwater foils’ induced drag, AND increases the span of the sail by making the longer leech more upright, which causes the sail to have less induced drag also. Appreciating the power of span squared can be useful when making decisions that affect performance.